1. Best Chipboard Screws for Furniture Making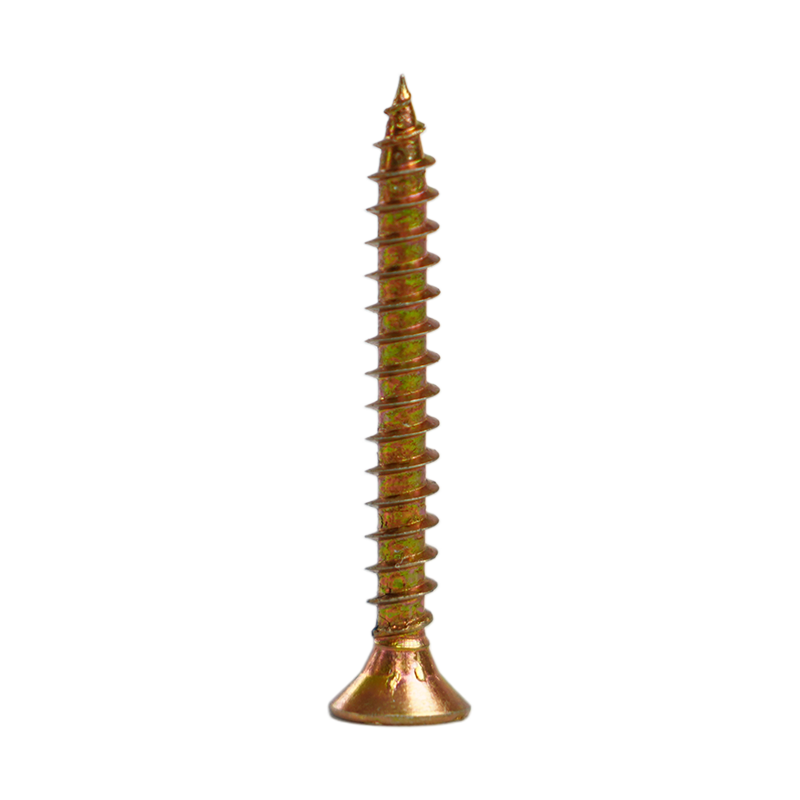
When it comes to constructing durable and long-lasting furniture, selecting the right fasteners is crucial. Chipboard screws are specifically designed to provide superior holding power in engineered wood products like particleboard, MDF, and plywood. Unlike standard wood screws, they feature a unique thread design that minimizes splitting while ensuring a tight grip.
- One of the key advantages of using chipboard screws for furniture making is their self-tapping ability. The sharp, aggressive threads cut into the material without requiring pre-drilling in many cases, saving time and effort. Additionally, their full-length threading ensures maximum pull-out resistance, which is essential for furniture joints that endure frequent stress, such as chair legs or cabinet frames.
Another important consideration is the screw's material and coating. Since furniture often requires a polished finish, opting for screws with corrosion-resistant coatings (such as zinc or ceramic layers) prevents rust and maintains a clean appearance. Furthermore, the screw head type—whether countersunk, pan head, or flat head—should be chosen based on aesthetic preferences and functional needs.
For heavy-duty furniture projects, thicker gauge screws with deeper threads are recommended, whereas finer threads work well for lightweight applications. When working with laminated chipboard, using screws with a reduced shank diameter near the head helps prevent surface cracking.
To summarize, the best chipboard screws for furniture making should have:
- Self-tapping design for easy installation
- Full-length threading for maximum grip
- Corrosion-resistant coatings for durability
- Appropriate head style for seamless finishing
2. Chipboard Screw Size Chart and Guide
Choosing the correct screw size is fundamental to the structural integrity of any chipboard project. A chipboard screw size chart and guide helps eliminate guesswork by providing precise measurements for different applications.
Understanding Screw Dimensions
Chipboard screws are typically measured by two key dimensions: diameter (gauge) and length. The diameter determines the screw's thickness, while the length must be sufficient to penetrate the material without protruding. Common diameters range from 3.5mm to 6mm, while lengths vary between 12mm and 150mm, depending on the project.
Selecting the Right Length
A general rule is that the screw should penetrate at least two-thirds of the bottom material's thickness. For example, when joining two 18mm chipboard panels, a 30mm screw ensures a secure hold without risking blowout on the opposite side.
Thread Pitch Considerations
Coarse threads are ideal for softwoods and chipboard, as they provide better bite and reduce the risk of stripping. Fine threads, on the other hand, are better suited for hardwoods where a tighter grip is needed.
Application-Based Recommendations
- Small fixtures & trim work: 3.5mm x 16mm - 25mm
- Cabinet assembly: 4mm x 30mm - 50mm
- Heavy-duty framing: 5mm x 70mm - 100mm
3. Self-Tapping Chipboard Screws vs Regular Screws
When working with engineered wood products, understanding the differences between self-tapping chipboard screws and regular wood screws is essential for achieving optimal results.
Design and Functional Differences
Self-tapping chipboard screws feature a uniquely sharp point and aggressive thread pattern specifically engineered to cut through dense materials like particleboard and MDF without requiring pre-drilling. The tip acts like a drill bit, creating its own pilot hole as it penetrates the surface.
Performance in Various Applications
The choice between self-tapping and regular screws depends largely on the project requirements:
- Furniture Assembly: Self-tapping chipboard screws excel in furniture construction because they provide strong holding power without the need for extensive pre-drilling.
- Structural Framing: While regular screws may be suitable for some framing applications, self-tapping variants are often preferred for chipboard.
4. Where to Buy High-Quality Chipboard Screws Online
Finding reliable sources for high-quality chipboard screws can be challenging, especially with the vast array of options available in the digital marketplace.
Key Features of Quality Chipboard Screws
Before making a purchase, consider these essential characteristics:
- Material Composition: Look for hardened steel or stainless steel constructions with corrosion-resistant coatings.
- Thread Design: Premium screws feature deep, sharp threads optimized for chipboard's fibrous structure.
5. How to Prevent Chipboard Screws from Splitting Wood
Splitting is a common issue when driving screws into chipboard or similar engineered woods. However, employing proper techniques can minimize this risk significantly.
Pre-Drilling: The Fundamental Solution
Creating pilot holes slightly smaller than the screw's core diameter is the most effective way to prevent splitting.
- Drill Bit Selection: Choose a bit 60-70% of the screw's shaft diameter.
- Depth Control: Drill to ¾ of the screw's length to allow the tip to engage fresh material.